Setting Calves up for Success: BQA specialist reminds producers of best management practices for branding and processing calves
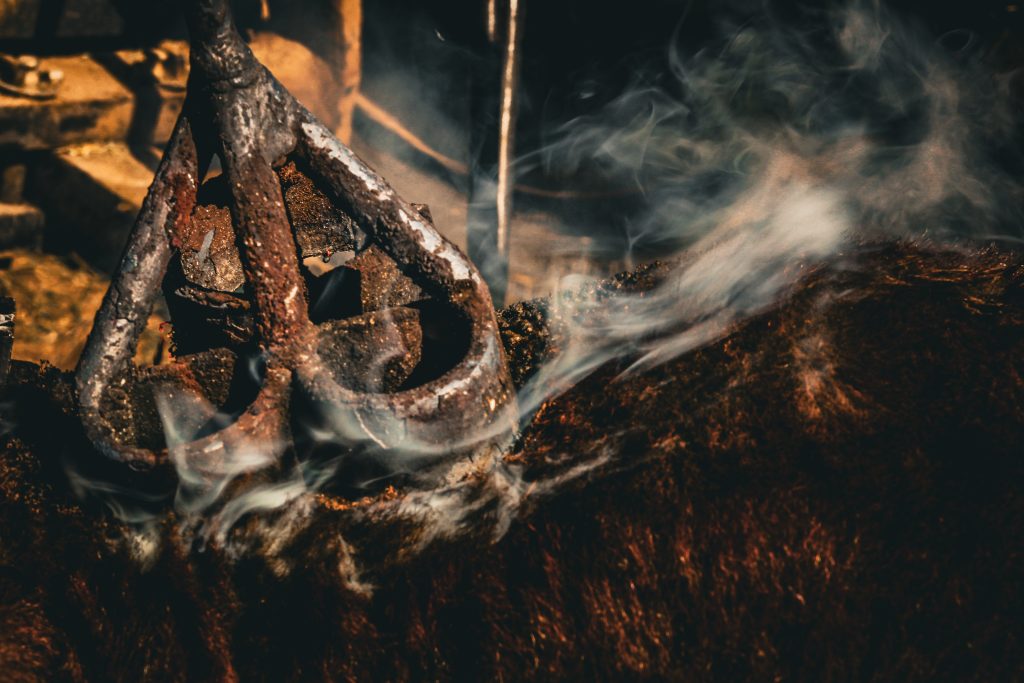
For producers with earlier spring-calving herds, the busiest time of year is now behind them, and they are moving on to the next big job – branding and processing their calves.
Although many cattlemen have likely participated in numerous brandings and processing days, University of Nebraska-Lincoln (UNL) Extension Educator and Director of the Nebraska Beef Quality Assurance (BQA) Program Jesse Fulton offers a few best management practice reminders for producers to consider in an effort to set their calves up for success.
VCPR and pre-examination
To begin, Fulton reminds producers it is important to establish a veterinary-client-patient relationship (VCPR), so their local vet can get to know them, their cattle and their operation.
“It is important for producers to have a VCPR so their vet can understand their herd and what they are doing on their operation, as well as the present health and disease challenges they might be facing,” he says during an April 20 UNL BeefWatch podcast, in which he sits down to discuss his corresponding BeefWatch Newsletter article titled “Calf Processing and Branding.”
In the article, Fulton writes, “Relevant information to examine prior to processing young calves includes current health status of the herd, previous health challenges within the same management and environmental constraints and operation goals for the vaccination protocol.”
Low-stress handling
For some operations, branding may be a big to-do, with family, neighbors and other members of the community invited to help with the work, get a glimpse into cattle production and likely enjoy a big meal.
With an outside labor force, usually representing different experience levels, Fulton encourages producers to clearly communicate their priorities and expectations so everyone is on the same page and to brief branding help on low-stress handling practices.
“Producers should visit with their help to refresh them on basic cattle handling do’s and don’ts on the operation,” he writes. “Additionally, briefing on expectations of cattle gathering, sorting and the steps to follow at processing is a good way to ensure everyone is on the same page.”
“Depending on branding methods, discussing the expected branding etiquette can improve the efficiency of the day,” he adds.
On the topic of low-stress handling, Fulton notes research from Oregon State University found the greatest contributing factor to increased cortisol levels in calves during branding was caused by separation from their dam, not from the actual processing method.
“So, the faster we can get them back with their moms, the less amount of stress we are putting on those calves,” he says. “Sufficient communication between all individuals present will lead to prevention of stress in all areas.”
Administering vaccines
Arguably the most important part of processing and branding calves is vaccine administration.
“Producers spend a lot of money on vaccine, so it is important they work the way they are supposed to when given to a calf,” Fulton says, further offering a few best management practices related to vaccination.
First, when using a vaccine that requires mixing, Fulton says it is important to only mix bottles as needed, no more than an hour before using it.
“If a problem arises preventing the crew from finishing the job, the efficacy of the extra vaccine will go down after one to two hours of being mixed,” he explains.
Another suggestion he offers when mixing vaccines is to not over shake the bottle.
“I understand the box says to mix well, but it is not what the manufacturers intended. They should probably say to mix well but mix gently,” Fulton says. “Simply swirling the vaccine in the bottle or swishing it back and forth a few times is enough to ensure a good mix.”
Fulton explains vigorously shaking the bottle can actually damage the vaccine by breaking bonds apart and releasing endotoxins which can be harmful to calves.
Next, he reminds producers to keep vaccines protected from the elements, store them according to the product label, avoid exposure to UV light and keep them from freezing.
“Most ranchers put their vaccines in a cooler directly next to an ice pack, and when they do this, the vaccinees can start to slush up or even freeze entirely,” he says. “There are some vaccines freezing will completely destroy, so it is my recommendation to try to stay as far away from letting them freeze as possible.”
Another of Fulton’s suggestions is to label syringes so they don’t get mixed up and to change needles every time a syringe is refilled.
“It is recommended to replace needles every 10 to 15 head, but if we are giving a product where we have to refill before we’ve treated 10 to 15 head, we should change the needle anyway,” he explains. “If we stick a dirty needle in the bottle, we can contaminate the rest of the vaccine.”
Lastly, Fulton reminds producers to give all injections in the neck in front of the shoulder, unless labeled otherwise.
He acknowledges this gets tricky for producers who hold calves on the ground when branding, but encourages them to look into different ways they can train their crew to hold calves down while also leaving the neck accessible to the person administering the vaccine.
“The last thing producers needs to do is make sure they are giving a product labeled for subcutaneous administration, because if we give an intramuscular vaccine, it can damage the muscle,” he concludes.
Hannah Bugas is the managing editor of the Wyoming Livestock Roundup. Send comments on this article to roundup@wylr.net.